Carli Suspension
Carli Extreme Duty Lifetime Ball Joints *Upper and Lower Set of 4* (13-24 Ram 3500/14-24 Ram 2500)
Carli Extreme Duty Lifetime Ball Joints *Upper and Lower Set of 4* (13-24 Ram 3500/14-24 Ram 2500)
Couldn't load pickup availability
Carli Suspension truly set a new precedent for upgraded ball joints for Heavy Duty Rams upon the release of their original lifetime guaranteed ball joints back in 2007. Their indestructible nature has proven themselves time and again when faced with hard core offroad abuse, oversized tires, or just your average Cummins sporting hundreds of thousands of miles. No matter the environment, you can try to wear them out, and you will fail. And if by some miraculous feat you can, Carli will send you replacements, simple as that.
INTRODUCTION: Since the release of the 2nd Generation series of heavy duty Rams back in 1994, Ram owners have fought against front end related steering and suspension related issues. Whether its merely a looseness in the steering wheel due to worn tie rods and gear box, abnormal tire wear, or even the Dreaded Death Wobble, Dodge went through numerous revisions of each and every part to correct the issues, and the aftermarket has reacted time and again with upgrades. Carli Suspension is one of those companies that has stepped up in a big way to make your Ram drive and steer like a Cadillac, even when thrashed offroad, or simply for that truck owner who wants to replace a part once and for all, then rack up a million miles.
WHAT MAKES THEM BETTER? The main differentiators that matter - materials, process, and design. The design comes first. To know how Carli reinvented the wheel, let's first take a look at the factory ball joints. The factory ball joints are made up of a lower ball joint and upper floating king-pin. What better way to learn a product than to cut it in half to learn it's functionality? The upper ball joint is designed as a pivot point determining the axis on which the knuckle will move and thus, only sees a lateral load. When you cut into the factory ball Joint, you find a sealed housing, sleeve, pin, and boot. The upper cavity stores the grease from the factory and allows the "hat" of the pin to float up and down as the knuckle raises and lowers through the steering cycle. The "hat" of the pin does not make contact with the housing, it only prevents the pin from pulling out the bottom of the housing. As the hat of the pin doesn't contact, there's a coated sleeve that isolates the pin from the housing and it's vertical surface is the only wear surface for the upper.
The Carli Joints are similar in design in that they utilize the same style of a floating king-pin upper, but with several improvements in design. You'll notice the Carli ball joint has a pin and housing, but the "hat" of the pin contacts the housing. This adds a second wear surface to further distribute the load applied laterally to the ball joint while providing the same failsafe as a factory ball joint, ensuring the pin cannot be pulled through the bottom of the ball joint housing. Further, there is no sleeve isolating the wear surfaces, eliminating the point of failure. The upper cavity's size is increased to hold a larger grease reserve and the threaded cap both allows access to the cavity and pin if needed and allows servicing through its zerk fitting. You'll also notice the channel in the pin itself providing a path for grease to migrate to the wear surface. At the bottom of the housing, a Viton Seal prevents the environment from entering the ball joint.
The lower ball joints are the true ball joints in the AAM design. The spherical lower is a ball and socket design allowing lateral misalignment (unlike the king-pin upper). Because the design tracks the knuckle on an imperfect axis, the spherical lower is required to allow the knuckle to move freely with only a slight vertical travel through its steering cycle. By design, the lower factory joint is a pin isolated from the housing by a nylon material loaded from the top and sealed by a press with a boot to keep out the elements. When this composite liner fails, the ball joint needs to be replaced. It's the old saying, a chain is only as strong as its weakest link.
The improvement on this design begins with the ability to service the joint. The Zerk fitting is recessed into the top of the joint and protrudes at an angle to be aimed forward and slightly inward to allow access to the fitting without needing to disassemble anything. In the cutaway, you can see the channels machined into the Carli ball surface conducive to grease migration. Again, you'll see no liners of any kind. At the top, a bronze wear surface preloaded by a disc spring, safety washer and snap ring ensures the ball joints wear surfaces are always held tightly together for optimal performance.
HEAT TREAT AND COATING: Now that the design improvements are clear, how is Carli so confident in the materials that they believe can eliminate wear-surface isolation? Simple, Carli has tested every possible material and process to land where they did since the inception of these lifetime ball joints in 2007. The process starts with masking. The ball joints are masked, all but the wear surface, with a copper plating. Once plated, the ball joints head to carburizing. The carburizing creates an extremely hard surface with a case-hardness (penetrating depth) of 20-25 thousandths. For reference, another process that was tried was salt-bath nitride, which produced 3 thousandths in a best-case scenario. When the ball joint has completed the carburizing/heat treat, they're stripped of their copper masking, leaving the entire joint heat treated and the wear surfaces incredibly hard. From stripping, they head to dry-lube where the whole joint is coated with a corrosion resistant gray coating to project the joint while the lubricity of the coating pairs with ant seize and Redline CV2 grease to assist in breaking in the wear surfaces.
MATERIAL COMPOSITION: Normally, this is where you list the recipe of materials - well, Carli won't spill the beans as it could mean their competition will have immediate access. The time they've put in (literal blood, sweat, tears) and hundreds of thousands of dollars to develop this indestructible product, have led them to safeguard this recipe with their lives.
LIFETIME WARRANTY: These ball joints are backed with the industry's only ADVANCED REPLACEMENT Lifetime Guarantee. Keep your purchase receipt and know you're set for the life of the truck. If anything should happen, shoot the crew at Carli a video of the play (Excess of .040" vertical or .020" lateral) and your purchase receipt and you'll have replacements en route with a call tag to return the defective joints; simple as that. When you receive the new ones, swap them in and send the old ones back with the included call tag. This process is more expensive, but it's a small price to pay to provide the best product and peace of mind that you'll be a Carli customer for life.
Share

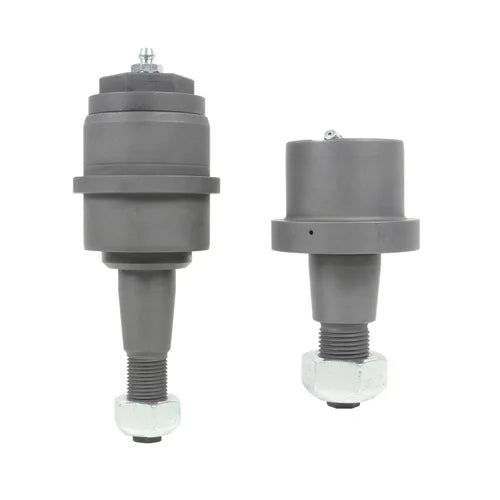
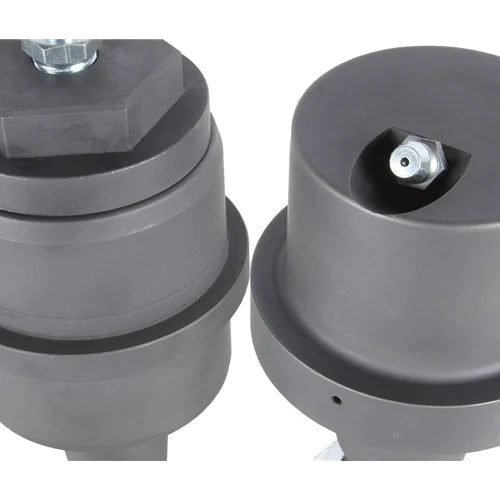
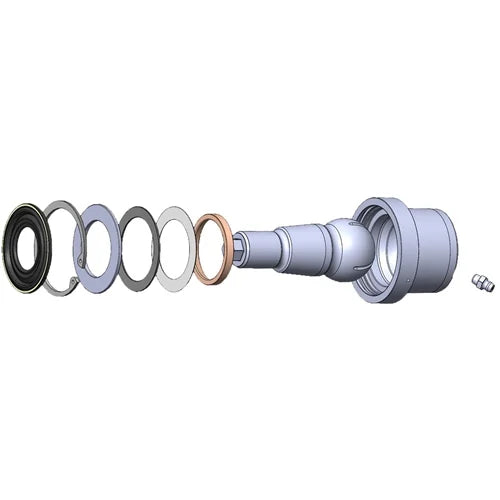